The company was established in 1970 by Mr. Tirabassi and Mrs. Vezzali, who then handed it over in 2013, to the current owners – myself, Luca Santelli, Marco Frignani and Simone Salsi.
The company started off as a subcontracting turnery, developing over time to eventually supplying finished products to its clients who were looking for a one-stop source for their orders.
We have an end-cutting department and from there we move on to the turning department, where we have nine CNC lathes and then five machining centres in the milling department.
We also have three hobbing machines, two of which are shapers for cutting the gears.
Our main sectors are agricultural mechanics, earth moving, the energy industry and, last but not least, the shipbuilding industry.
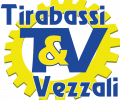
Over the years we have invested in lathes that can turn parts up to 1,200mm long, and with machines like these it was obligatory to invest in testing systems for the parts.
We bought a new generation VICIVISION machine for the precision because, at the end of the day, it’s the best on the market.
Nowadays, client requests are increasingly specific and so we needed to find a reliable partner.
Each operator has his own barcode, he scans the program code on the project and carries out the inspection automatically, so neither I nor a Quality Manager need to be there.
The main benefits of this machine are speed – inspections are much faster than previous manual systems – and an objective inspection of all the details, regardless of who is actually checking the part.
This machine is essential for our work because all the operators know that they can trust the results.